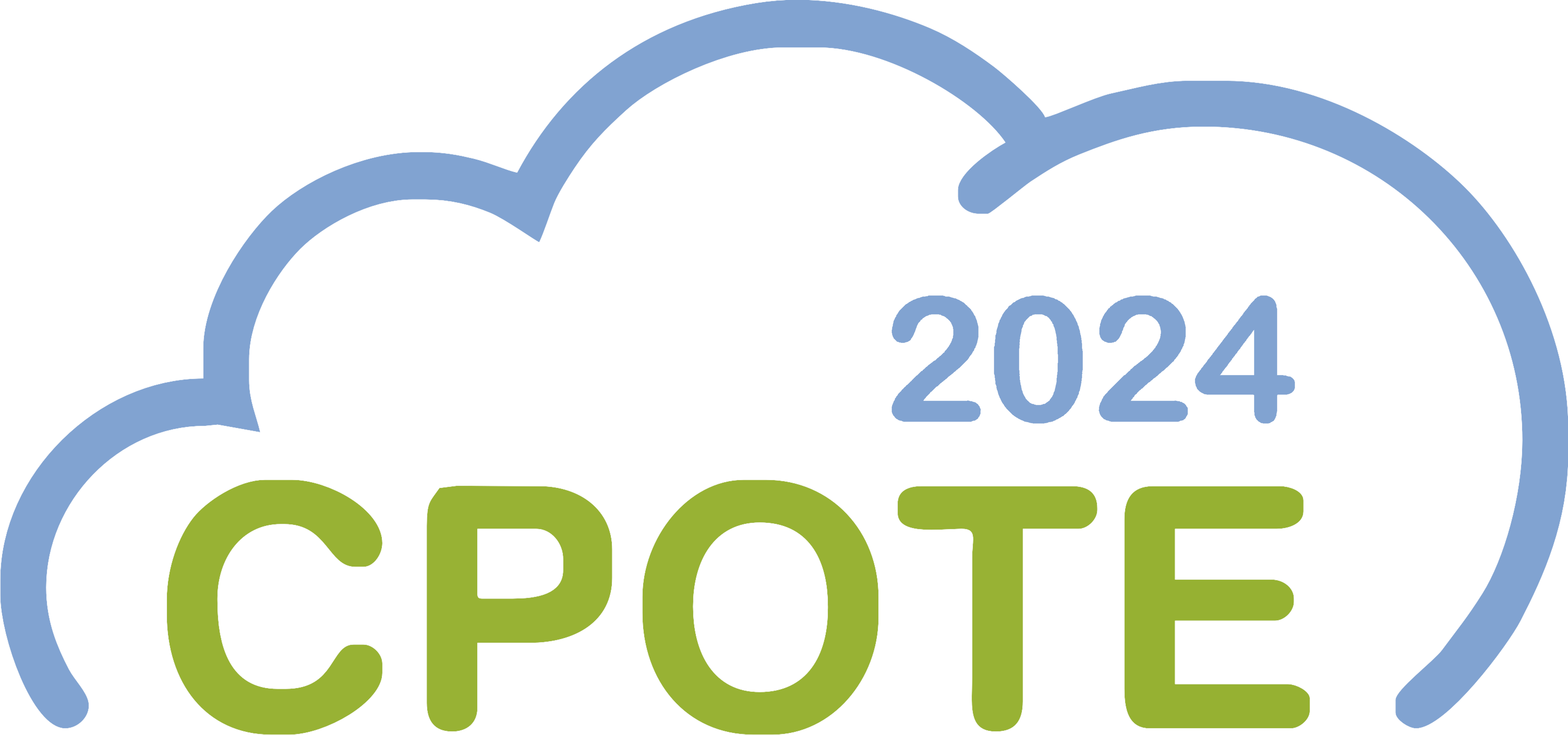
CPOTE2024
|
8th
International Conference on
Contemporary Problems of Thermal Engineering
23-26 September 2024 | Gliwice, Poland | Hybrid event
Contemporary Problems of Thermal Engineering
23-26 September 2024 | Gliwice, Poland | Hybrid event
Abstract CPOTE2024-1019-A
Three-dimensional analysis of centrifugal compressor stage performance with methane-hydrogen mixtures
Murillo PEREIRA NETO, University of Sao Paulo, BrazilJurandir YANAGIHARA, University of Sao Paulo, Brazil
The growing importance of hydrogen (H2) in decarbonization initiatives has spurred interest in aerodynamic design and analysis of radial compressor stages, crucial for transporting both pure H2 and H2-natural gas mixtures through pipelines. Although thermodynamic studies abound, comprehensive Computational Fluid Dynamics (CFD) analyses in this domain are scarce. This work investigates the impact of varying hydrogen fraction (0%, 10%, 20%) on the performance of radial compressor stage. The stage, comprising an impeller and vaned diffuser initially designed for pure methane operation, undergoes thorough CFD analysis. Geometry is generated by a radial compressor design code based on the 1D meanline and 2D streamline curvature methods. Results at design rotation speed show that higher H2 fractions reduce stage pressure ratio (1.758 to 1.567), efficiency (-0.38%), while volumetric flow rate is kept approximately unchanged. Results at higher rotating speeds show that similar pressure ratios are attainable if blade tip Mach number similarity is ensured. Nonetheless, performance degrades under such conditions: isentropic efficiency decreases (-0.27%), operating range decreases (1.29 to 1.03 kg/s), and mass flow choke margin decreases (0.99 to 0.23 kg/s). Detailed three dimensional analyses reveal intensified boundary layer and mixing losses within the vaned diffuser due to higher H2 content, notably at midstream near the pressure side, midstream at hub near the suction side, at channel discharge, and downstream trailing edges. Consequently, while radial compressors exhibit versatility in handling varying gas compositions, performance degradation is inevitable. This underscores the need to design compressors tailored to representative compositions to mitigate losses, especially as the operation deviates from design conditions.
Keywords: Computational fluid dynamics (CFD), Centrifugal compressor, Turbomachinery design, Natural gas - hydrogen mixture, Hydrogen
Acknowledgment: We gratefully acknowledge funding for this work from São Paulo Research Foundation (FAPESP) grant 2023/06391-3.